Blog
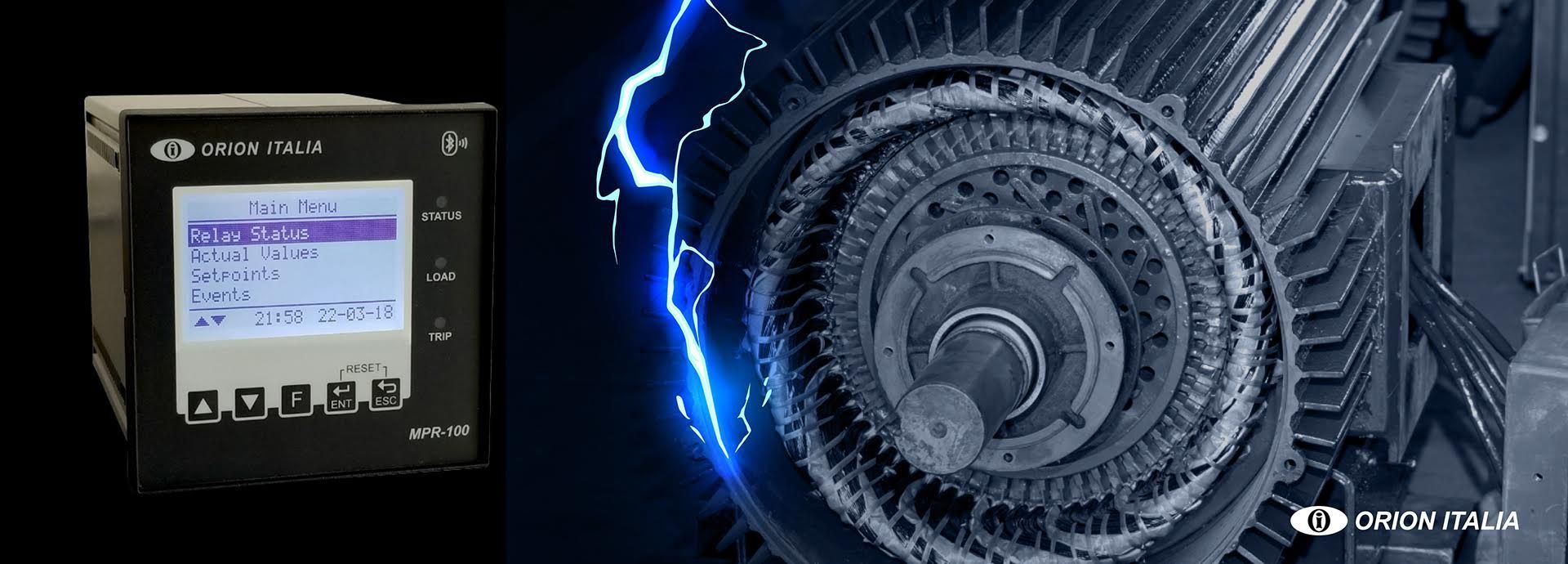
What Damage Do Current Overloads Cause in Asynchronous Three-Phase Motors?
Asynchronous Three-Phase Motors, capable of triggering a sequence of unfavorable events that jeopardize the equipment's structural integrity and its operational efficiency. In an era where real-time monitoring and predictive maintenance are increasingly prevalent, understanding the ramifications of these events is essential for optimizing motor lifespan and reducing downtime.
The negative Consequences of Overheating
Overheating arises directly from current overloads. When a motor exceeds its rated capacity, the internal resistance of the windings increases, which converts electrical energy into heat. This scenario leads to multiple problems.
Decreased Energy Efficiency
The motor's efficiency is reduced by the excess heat generated from overload currents, leading to higher energy consumption for accomplishing the same work, thereby elevating operational costs.
Accelerated Aging of Components
High temperatures hasten the wear and tear of crucial motor components such as insulators and lubricants, which may shorten the motor's useful life.
Mechanical Stress Due to Thermal Expansion
Disproportionate expansion of motor components from heat can lead to internal misalignments, which can increase the rate of wear and the likelihood of mechanical failures.
Extreme Motor Damage
In the most severe cases, the intense heat from overloads can cause devastating damage, including the melting of windings or, in the worst scenarios, fires.
Insulation Integrity & Motor Safety
Subsequent to overheating, insulation integrity is the next significant concern. The safe operation of any electric motor relies on the condition of its insulation:
Short Circuits
Weakened insulation can cause short circuits within the motor windings, increasing the current and generating additional heat, perpetuating a harmful cycle of degradation.
Earth Leakage Risks
Deteriorating insulation may lead to current leakage to earth, creating a hazard of electric shock and potentially triggering protective devices that could interrupt motor operation.
Weakened Dielectric Strength
Once insulation integrity is undermined, the motor's ability to endure electric voltages without arcing or leakage is compromised, putting the equipment's consistent performance at risk.
Proactive Maintenance: Transforming Electric Motor Management
In the digital era, marked by the proliferation of the Internet of Things (IoT), the role of telemetry and advanced analytics in preempting and pinpointing operational issues is more pivotal than ever.
Leveraging cutting-edge solutions like Artificial Intelligence (AI) and Machine Learning (ML), we can now sift through operational data with unparalleled precision and speed.
This real-time analysis uncovers emerging trends and potential precursors to current overloads, along with their implications. As a result, there is a paradigm shift from traditional reactive maintenance to a forward-thinking, proactive strategy.
This proactive maintenance prioritizes the early detection and immediate rectification of irregularities, dramatically reducing downtime and significantly enhancing the reliability and longevity of these essential electric motor assets.
The Solution to Overloads in Asynchronous Three-Phase Motors
In this context, Orion Italia stands out as a strategic ally. We specialize in manufacturing advanced relays that not only detect current overloads but can also be programmed to initiate corrective actions or send alerts in the event of any anomalies. Our devices represent a synthesis of innovation and quality, backed by the Made in Italy guarantee.
Integrating our relays into your electric motor system is a step
forward towards optimizing safety, efficiency, and reliability.
SHARE THIS ARTICLE
Discover More